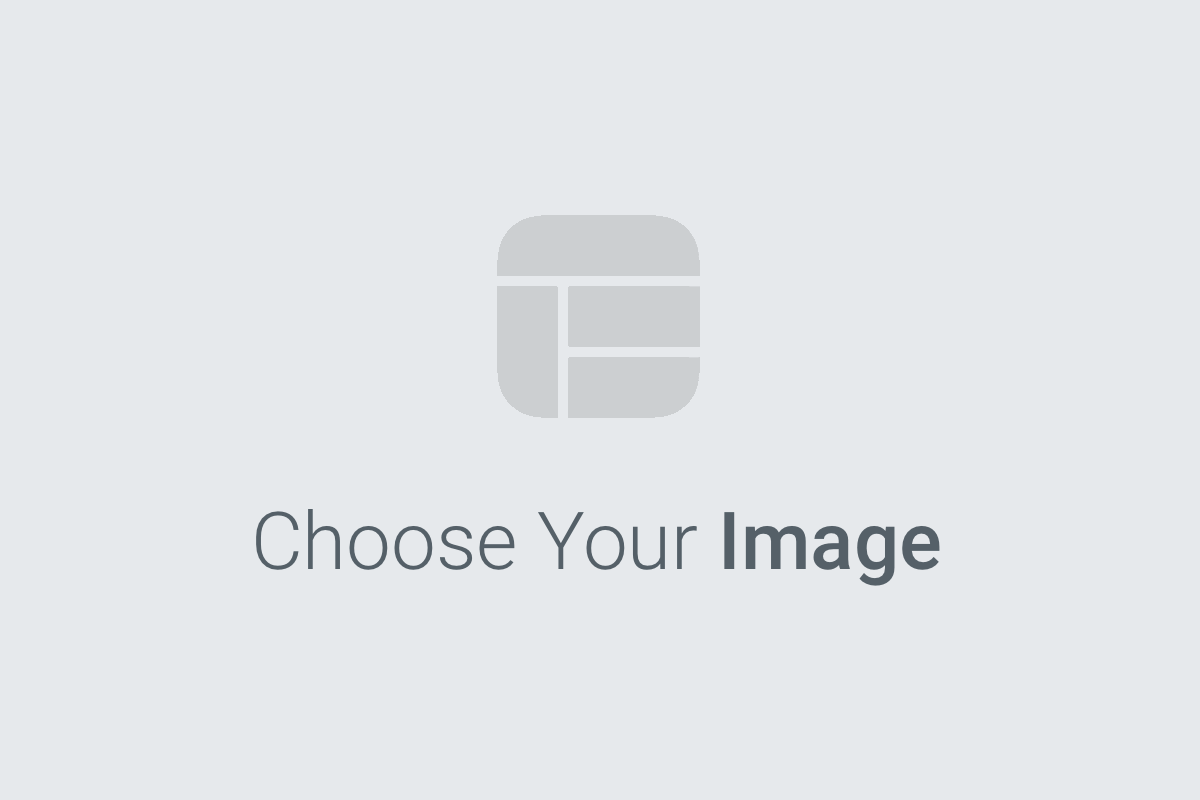
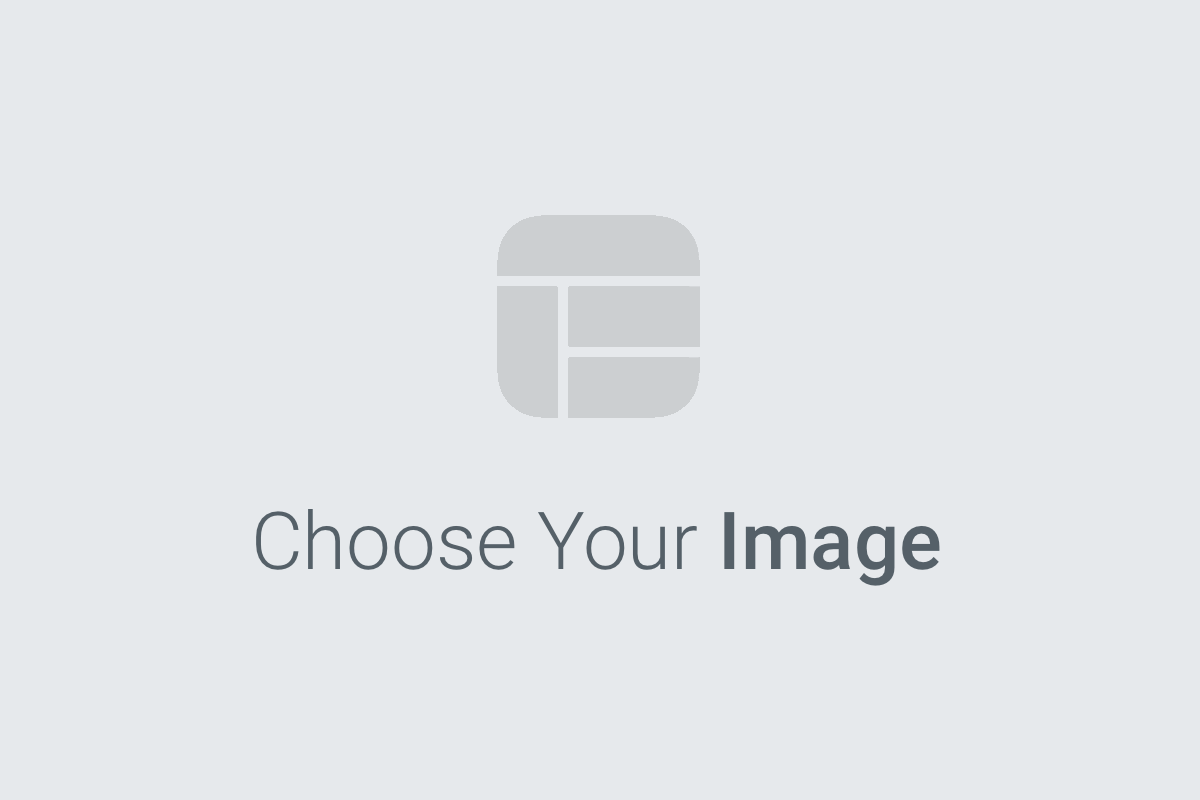
Menu
Menu
The Club collects information from all amateurs of knife-makingIf you want to speak about something important for you, don't hesitate contact us.
Steel is an alloy of iron and carbon. An alloy is a combination of several factors, most of which time metal have different properties of each original member.
Steel can be obtained directly after reduction of iron ore in a blast there, it is natural steel.
It is possible to burn the extra carbon in the molten iron in order to reduce its rate.
Mixing a carbon-rich cement (as crushed horn or charcoal) and iron ore is heated to a temperature below the melting point (about 1200 ° C), for about ten hours (but time is always dependent on the dimensions of the workpiece) in a refractory clay oven having holes for the admission of air.
The oxygen in the air and cementum give dioxide and carbon monoxide.
There is removal of oxygen, that is to say the reduction of iron ore (which is an oxide, Fe2O3) to metallic iron by the carbon monoxide.
Are obtained porous cells which descend in the furnace to form a slurry of sponge iron.
Soluble carbon in this element dissolves somewhat and hardens iron to transform the steel.
After purification of the hammer to sponge iron (iron hammered), pig iron particles are obtained with low carbon content.
Then increased its content of heating small pieces of iron with a new injection of cement in a clay pot (8 cm diameter and 16 cm high) that is sealed to prevent the iron reoxidizes to air.
When lapping indicates the presence of molten material, the crucible is cooled very slowly in the oven.
Blacksmiths heat the entire 1200 ° in a stone oven.
The carbon content in the cement reacts with the oxygen of the iron ore which is thus eliminated.
Above 727 °, the metal is still solid and a crystalline lattice is formed by the repetition of patterns having cut an iron atom at the center of each face; carbon diffuses gradually in this structure and the atoms are deposited onto the gaps between the iron atoms.
The addition of carbon lowers the melting point of the metal.
When the carbon content exceeds 2% in the surface of the pieces of iron, a thin molten layer of white iron is formed on the pieces.
Blacksmiths shaking the crucible for the presence of the melt; if they hear a kind of lapping, this means that a good proportion of carbon is dissolved in the iron.
Smiths cool the crucible to room temperature very slowly, sometimes over several days.
Thus, the iron atoms are placed at the center of each cube, leaving little space for carbon atoms.
This ensures an even distribution of the carbon in the entire mass of steel.
(The final overall carbon content is between 1.5 and 2% when it was expected to have the molten layer of white iron.)
When the pot temperature drops - below 1000 °, a part of carbon precipitates and forms a network of cementite, or iron carbide (Fe3C), around the grains of austenite.
As the cooling is slow, the austenite grains have time to grow and cementite network is rude.
Cementite is extremely hard but extremely brittle at room temperature.
The mesh cementite exacerbates the fragility of the steel thus has drawn any fracture lines.
Depending on the proportion of cement in the mixture is obtained from pig iron with very low carbon content of the melt to more than 4% carbon.
The result is broken after cooling and observation breaks classifies the pieces in order of carbon content.
After selecting small pieces and drop them on an iron pallet (equipped with a tail for easy handling)
heated to 1100 ° and homogenized by hammering.
A first central part is forged and is added the iron pieces soaked in water that had been previously hammered and which are in the form of small particles that are welded to the central part, while a transformant sheet.
Resistance requested by the cutlery steel requires purification by mechanical, thermal or chemical.
It is necessary to remove non-metallic inclusions in steel which are actually dirt trapped in the matrix that have not undergone the same transformations during tempering the metal structure.
These are all soft areas that affect the hardness of the blades and brittle.
Cutlers directly using bars or steel bar ends.
The bar is the state where most steels are sold.
They come in square or rectangular (in which case it is called flat).
Cutlers mainly use steel that form.
- The pre-formed bars, triangular or rhomboid section (for double-edged blades) are used to save time on the manufacture of the blade.
- The end of bar: the hammering of the tip of the truncated pyramid-bar in order to extract the part to be forged.
Iron comes after forging bar that is to say, in large ingots Diamondbacks.
Selected its ends, the blacksmith could extract the metal as its needs.
Steel can also be in other forms such as small ingots the size of a hockey puck.
Our knives are usually fitted with a 12C27 stainless steel blade. However, for each model it is possible to insert a carbon steel blade. This option can be chosen at the 4th stage of our personalisation module. It is only possible to choose a Laguiole with Damas steel blade for certain types of handle.
check_circle
check_circle